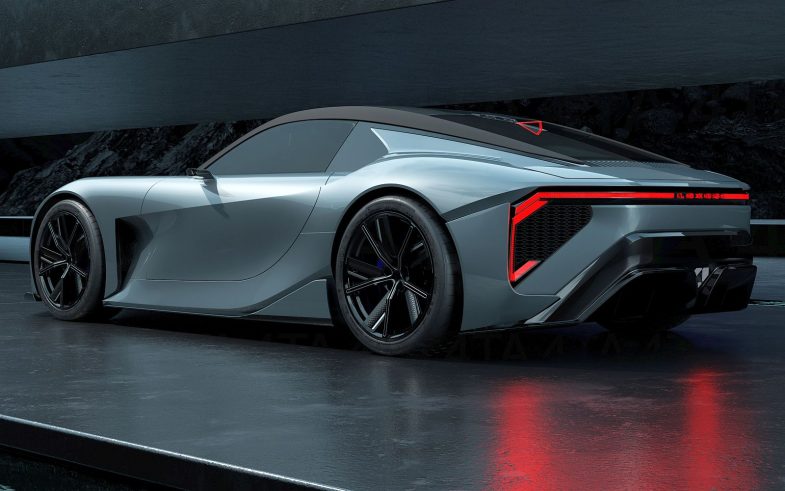
What is the Lexus Sport Concept?
Does the Lexus Sport Concept offer clues to a potential new sports car, even a successor to the iconic Lexus LFA? Here’s the official answer.
Click to read about Lexus cars & more, including our range of electrified vehicles and the philosophies underpinning our brand.
Does the Lexus Sport Concept offer clues to a potential new sports car, even a successor to the iconic Lexus LFA? Here’s the official answer.
From 27 August to 6 September, the Venice Lido will become a crossroads between cinema and automotive innovation as Lexus illuminates the city following its announcement as the official car and sponsor […]
What do professional road testers think of our flagship e-SUV’s improved power, efficiency and performance? Read their 2026 Lexus RZ reviews.
Tennis stars Jamie Murray and Laura Robson ‘served at speed’ in an epic car rooftop stunt that pushed the sport to two new world records.
Introducing the extended, all-electric 2026 Lexus RZ line-up, offering more power, efficiency and dynamic performance with increased driver rewards.
Experience amazing with some refreshingly different UK spa recommendations that will help rejuvinate the mind, body and soul.
“This is my first Lexus. I’ve had it for almost a year and have become quite attached to it. I won’t be getting rid of it any time soon. It’s just a […]
What are the latest features of Climate Concierge, and how does it keep a comfortable cabin environment regardless of the outside temperature?
We talk to the gold medal-winning wheelchair tennis player Alfie Hewett about his success in the Paris 2024 Paralympic Games and life as a Lexus ambassador.
Our regularly updated review of the awards, achievements and accolades bestowed on Lexus UK’s cars, services and people during 2024.
We’ve refreshed and extended the 2025 Lexus UX 300e range for greater customer choice. Here’s an overview of the revised line-up.
“I find it’s such an easy car to own; arguably easier than a conventional car. I’ll never have to endure the smell of diesel on my hands or shoes again.” Richard Critchlow […]
We do everything in our power to make owning a Lexus an amazing experience. We aim to create a first class ownership experience, which includes bespoke services designed to take care of […]
Members of the UK motoring press were recently invited to test-drive the newly announced Lexus RZ 300e – the latest addition to the RZ luxury SUV line-up. You can read what they […]